1 Status
There are many blind holes in the cylinder block and the cylinder head of the engine, and the processed chips are deposited on the bottom of the hole, and often adhere to the thread groove together with the oil stain, and the chip cleaning work is very difficult. Generally, compressed air is used to blow off or high-pressure water to wash. These methods make the chips fly around, which is neither safe nor unsanitary. More importantly, the chips are not cleaned cleanly, resulting in poor cleanliness of the engine and extremely harmful, directly affecting the product. performance. For example, the residual chips in the threaded hole (blind hole) of the main bearing of the cylinder will cause the false moment of the main bearing bolt moment. After the engine runs for a period of time, the bolt will loosen, and the chip will easily enter the back of the main bearing bush, causing the main bearing tile to be squeezed and burned. Tiles, even the crankshaft is broken, and the engine vibration is large and other undesirable phenomena. If there is residual chip in the threaded hole for connecting with the cylinder head on the top plane of the cylinder block, the cylinder head bolt will also have a false moment phenomenon. When the engine is running for a period of time, the cylinders will be mutually suffocated. Ablation of the cylinder head gasket seriously affects the performance of the engine.
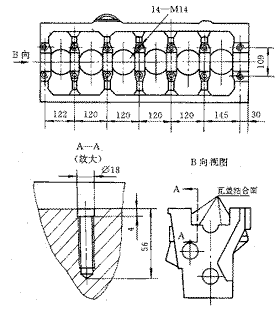 Figure 1 Schematic diagram of the threaded hole distribution of the main bearing of the cylinder |
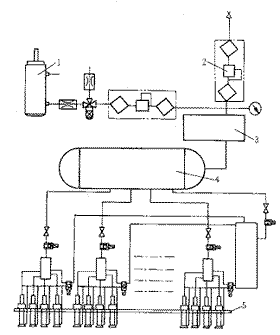 1. Cylinder 2. Filter device 3. Booster valve 4. Gas storage device 5. Pump body integrated board Figure 2 Schematic diagram of special pneumatic chip removing device |
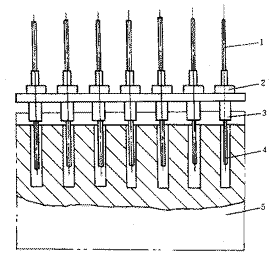 1. Air supply tube 2. Small pump body 3. Suction tube 4. Blow tube 5. Cylinder block Figure 3 Schematic diagram of the special pneumatic removal chip removal device |
2 Analysis of the original process plan
We take the machining process scheme of the threaded hole of the main bearing of the cylinder as an example for analysis. The threaded hole of the main bearing of the cylinder is used to connect and fix the main bearing cover and the cylinder. There are 14 in total, which are symmetrically distributed in the cylinder. On the bottom surface of the gantry (Fig. 1), the threaded hole is M14 and the hole depth is 43.8 mm. The main bearing threading hole is processed by the threaded bottom hole—tapping thread-milling cover joint surface (commonly known as dragon facade)—hydraulic pressure test (detecting water jacket leakage)—cleaning cylinder body—blowing threaded hole and tile cover Bonding surface - assembly of the main bearing tile cover. After tapping the threaded hole, the chip is bonded to the coolant and the lubricating oil and adsorbed in the threaded hole. When the joint surface of the tile cover is subsequently finished, the hot chip is also dropped into the threaded hole and sintered in the hole. The statistical results show that the oil chips in each hole weighs about 100g, and are blown away by compressed air. The chips will fly everywhere, the oil and water will be everywhere, the danger is great, and the working environment is poor. In order to reduce the above hazards, after the hydrostatic test, the high pressure water of the washing machine is used to clean the outer surface of the cylinder, the inner cavity and the threaded hole, so that the sludge in the threaded hole is reduced as much as possible, but the chip in each hole is still about 25 g. Then, it is blown off with compressed air. After checking by the magnetic suction rod, most of the chips in the hole are not cleaned up, which can not meet the product requirements. There are other disadvantages in this blowing process: the blown chips fly into or fall into other holes, destroying the cleanliness of other holes; the chips splashing around, not only causing safety accidents to the operator and surrounding humans; It is difficult to collect, resulting in poor sanitation; when passing the hydraulic test process and the cleaning process, the chips and sludge in the threaded holes can easily prematurely contaminate the hydraulic test liquid, the cleaning liquid and the rinse liquid, so the test liquid must be replaced. The cleaning liquid and the rinsing liquid increase the production cost; in addition, the whistling sound of the compressed air is particularly large; the worker has to manually remove the chips of the 14 holes and the tile cover joint surface at a time, the production efficiency is low, and the working environment is poor. Labor intensity is high; the phenomenon of leakage is also happening from time to time. 3 Development of a new blind hole chip removal machine
In response to the above problems, we borrowed the successful manufacturing technology from abroad and used the Venturi principle to design and manufacture a special and efficient device to remove all the chips in the 14 bolt holes at a time (Figure 2). When the workpiece is positioned (and the clamping mechanism can be added if necessary), the lifting cylinder 1 raises the small pump body integrated plate 5 to the working position, and the compressed air with a lower pressure (about 441 kPa) is filtered, and then the supercharger is used. The pressure is increased to about 834 kPa, and the two air pipes are diverted to 14 small pump bodies. The air flow in each small pump body is also divided into two paths. One of the gases leads to the blow pipe deep into the bottom of the threaded hole, and the deposition is deposited. The bottom or the debris adsorbed on the wall of the hole; the other gas is directed into the suction pipe at the threaded hole to cause vacuum suction (Fig. 3), and the chips in the threaded hole are completely sucked into the set. Inside the chip box. In addition, PC programmable control is used in electrical, which can adjust the blowing order and blowing time of each hole arbitrarily for best results. 4 Application effect analysis
- Technical effect
- Good process step prior to pressure, through a threaded hole debris strength blind bore chipper suction after addition, the presence of almost no chips; a small amount of sludge, and then by washing, drying at high temperature, not only the threaded hole of debris , and effectively prevent the Screw hole from rusting due to moisture (the moisture content of the compressed air in the original blowing process is extremely large);
- High production efficiency After adopting the new technology, the worker only needs to push the cylinder into position and press the button to complete the cleaning of the chips in 14 holes, and the production efficiency is high and the cleaning effect is ideal.
- Economic effect
- Reduce the production cost. Because the debris in the threaded hole passes through the pneumatic blind hole to remove the chip, the small amount of residual sludge in the threaded hole, when passing the hydraulic test process and the cleaning process, the hydraulic test solution, the cleaning solution and the rinsing The degree of contamination of the liquid is small and the replacement cycle can be extended. I have to change it once every half a month, and now I change it once a month;
- Reduced waste After half a year of trial production, from the feedback information on the engine assembly line, there is no phenomenon of false torque due to chipping in the threaded hole, and the repair rate is reduced to about 3%.
- Environmental protection effect
- The environment is good. The sucked chips are collected in the drawer under the bed, which does not affect the surrounding sanitation; the noise of the compressed air blowing during working is very small.
- Good safety After eliminating the swarfing process, the splattering of the swarf is eliminated and the unsafe factors are eliminated.
Tapping Screw
Although there are many types of tapping screws, they all have the following similarities:
(1) are generally made of carbonized carbon steel (accounting for 99% of total production). It can also be made of stainless steel or non-ferrous metals.
(2) The product must be heat treated. Carbon steel tapping screws must be carbonized and stainless steel tapping screws must be solution hardened. In order to make tapping screws to meet the requirements of the standard of mechanical properties and performance.
(3) The product surface hardness is high, the core toughness is good. That is, "soft inside strong outside". This is a major feature of tapping screw performance requirements. If the surface hardness is low, it can not be screwed into the matrix; If the core toughness is poor, a twist will break, can not be used. So "inside soft outside steel" is self-tapping screw to meet the use of performance, very important requirements.
(4) The surface of the product needs surface protection treatment, generally electroplating treatment. Some product surface must be treated by phosphate (photostatting), such as wall panel self - tapping screws for photostatting.
(5) Production by cold heading process. It is recommended to use high-speed cold heading machine and high-speed wire rolling machine or high-speed planetary wire rolling machine. High speed is emphasized here to ensure product quality. Only the head of tapping screw produced by high-speed machine is well formed and the thread quality is high.
Round head Tapping screw,hex tapping screw,flat head tapping screw,pan head tapping screw,truss head tapping screw
Shenzhen Lanejoy Technology Co.,LTD , https://www.wire-spring.com